Process that we do
Before the casting process begins, we perform several critical steps. A number of checks are performed before casting begins, such as inspecting raw materials, testing sand mixtures, and examining cores and modulus. The casting process ends with the final inspection of the product.
Aluminum Pressure Die Casting Process
Metal components that are net-shaped and have tight tolerances can be fast, reliable and cost-effectively manufactured using pressure die casting. Pressurized die casting involves injecting molten metal alloys under high pressure into steel molds (or tools). A net-shaped component is formed by rapid solidification (up to milliseconds). This is followed by an automatic extraction process.
There are two types of pressure die casting.
- High Pressure Die Casting
- Low Pressure Die Casting
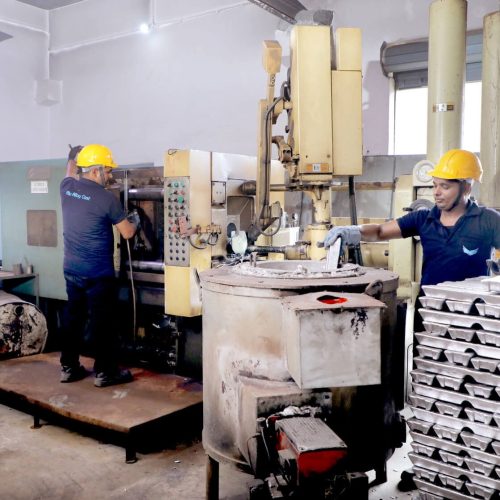
High-speed and high-pressure injection of liquid metal into metal molds is performed here. There are two vertical platens in the equipment. These platens collect the die halves and place bolsters on them. A fixed platen and a mobile platen make up the two platens.
By doing so, the die can open and close more easily. The shot sleeve is filled with a specific amount of metal, then the cavity of the mold is filled with the metal. Hydraulic pistons are used to accomplish this. It is then necessary to open the die and remove the casting after the metal has solidified.
There are two types of High Pressure Die Casting.
- Hot Chamber Process :
Metal pots, cylinders, and plungers cannot be eroded by the hot-chamber process, which is only applicable to zinc and other alloys with low melting points.
- Cold Chamber Process :
The injection system isn’t submerged in metal as with the hot-chamber process. By contrast, metal is transferred manually or automatically to shot sleeves by ladle.
In this process, aluminum alloy castings, magnesium alloys and other low melting point alloys are usually produced. It is common to find aluminum castings weighing between 2 -150 kilograms.
The first step is to place a metal die over molten metal in a sealed furnace. Molten metal is pushed into the molten metal through a riser lined with refractory. An air is then introduced into the furnace at a low pressure (15 – 100 kPa, 2 – 15 psi). This reduces the amount of turbulence in the die cavity as it rises up the tube and enters the die cavity. It is then necessary to release the air pressure after the metal has solidified.
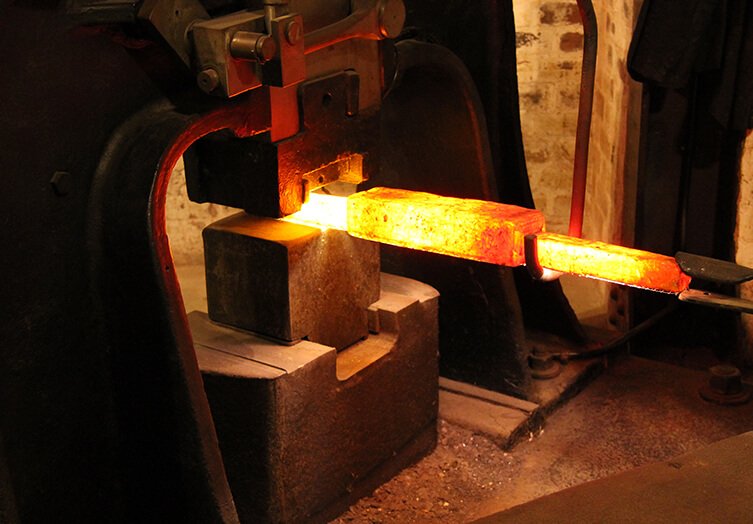
Aluminum Forging Process
Infrared heating is applied to the process of making Aluminum Hot Forgings, resulting in enhanced material properties: fatigue life, fine grain aluminum metallurgy, and hardenability. In order to reduce energy consumption and reduce costs, Queen City Forging uses infrared heating technology.
The Rapid Infrared (RI) heating process can reduce heating times by an order of magnitude, decrease energy consumption by a factor of three, and make forgings with superior mechanical and metallurgical properties in comparison to conventional heating processes.